
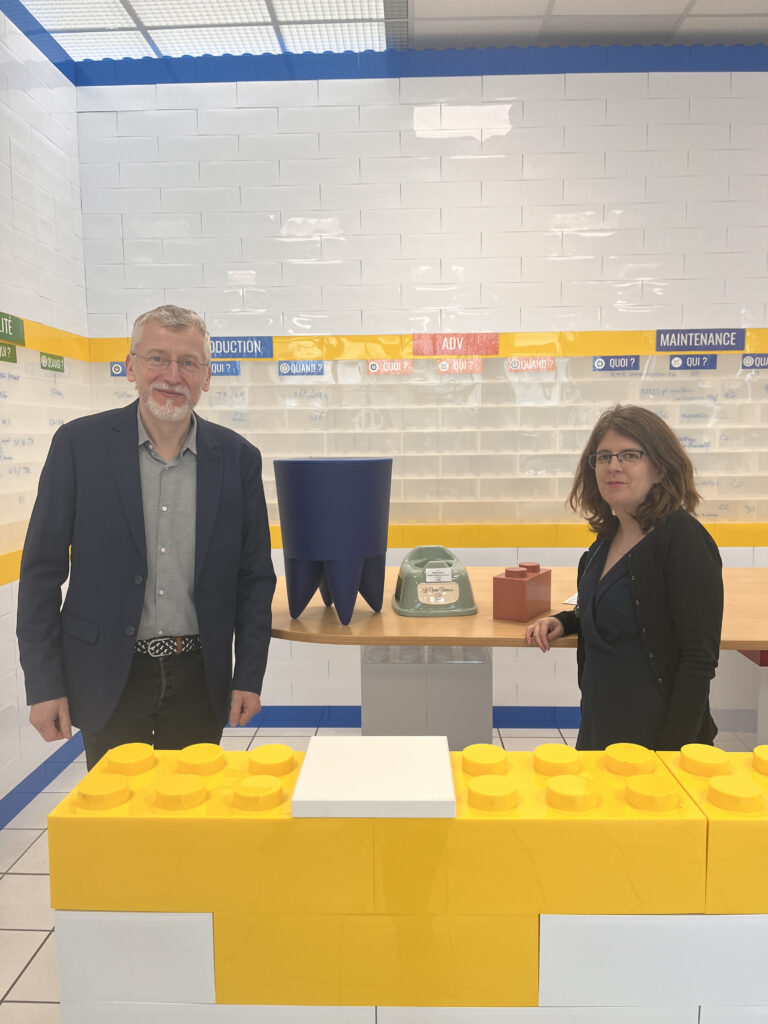
Depuis plus de cinquante ans, l’entreprise Ïoképlastic transforme des matières plastiques. Du célèbre tabouret du designer Philippe Starck au pot fabriqué par Le Biberon français, en passant par les accoudoirs des avions et les turbines de climatiseurs, l’expertise de l’industriel est connue et reconnue en France et à l’international.
Fondée en 1973 par la famille Collier à Langeais, la société initialement appelée « Plastique 2005 » est spécialisée dans la transformation de matières plastiques de petites et moyennes séries. En 2001, l’entreprise s’installe à Savigné-sur-Lathan (37). En 2017, l’entrepreneur David Rigaud la rachète et lui offre un second souffle. Son nouveau nom, Ïoképlastic, est d’ailleurs inspiré du nom d’une déesse grecque signifiant « qui ne renonce jamais ».
72 employés et 20 presses à injecter plus tard, l’entreprise réalise un chiffre d’affaires de 7 millions d’euros en 2023.
Plus de 50 ans d’expertise
« Si 80 % de notre clientèle est en France, nous travaillons également à l’étranger : Tunisie, Inde, Corée du Sud, ou plus récemment en Amérique du Sud. Aujourd’hui nos premiers clients sont des distributeurs et industriels de l’aéronautique, suivis de près par ceux du médical, de la puériculture et de l’industrie », indique Raoul Notter, directeur commerce et développement chez Ïoképlastic.
Pour l’aéronautique, l’entreprise produit des tablettes, des accoudoirs d’avion et des boîtes de gilet de sauvetage. Ïoképlastic est également sollicitée pour la réalisation de composants de turbines d’aération et de climatiseurs par des marques comme Carrier (spécialiste des systèmes de climatisation), et pour celle des moules à fromages Servi Doryl (spécialisée dans la fabrication fromagère). « Nous fabriquons également de nombreux produits pour la puériculture, s’enthousiasme Amélie Garnero, assistante commerciale. En sus de rehausseurs, pots et réducteurs, ce sont près de 60 000 poubelles à couches qui sont fabriquées chaque année pour la marque Angelcare. »
Le designer Philippe Starck fait également appel à l’entreprise pour fabriquer son célèbre tabouret « Bubu 1er », disponible en 80 couleurs.
Le design n’étant pas que l’apanage des clients, Ïoképlastic a développé des briques géantes baptisées « Brick-it ». Modulaires à 100 %, faciles à installer et à empiler, elles sont réutilisables à l’infini pour des services allant de la décoration à l’événementiel.
L’essor des matériaux biosourcés
« Depuis huit ans, nous travaillons avec des matériaux biosourcés comme la cellulose, les coquilles d’huîtres, les épluchures de pommes de terre, etc. Ils sont utilisés par exemple pour la vaisselle de traiteurs. Si actuellement ces matériaux ont un coût plus élevé que les matériaux fossiles, la décision finale appartient au client, indique Raoul Notter. Il nous revient de lui proposer des solutions adaptées à son cahier des charges. »
Dans un contexte de hausse des coûts, l’entreprise a adhéré au Groupement d’achat des acteurs du monde de la plasturgie (GAP) pour sécuriser ses achats. Parallèlement, elle travaille également en coopération avec le Groupement des industries françaises aéronautiques et spatiales (GIFAS). Cette fédération lui permet d’avoir une vision complète sur les tendances du marché et les prochaines évolutions technologiques.
Enfin, depuis le 19 mars dernier, Ïoképlastic a intégré l’accélérateur de transition écologique de BPI. Amélie Garnero précise que « cet accompagnement est une occasion de rencontrer des confrères, d’observer ce qui se fait et de pouvoir travailler à rendre notre activité plus durable ».
Ïoképlastic est résolument ancré dans le présent et tourné vers l’avenir !
www.iokeplastic.com
www.brick-it-france.fr
Présence au salon FIP de Lyon du 4 au 7 juin 2024
Camille Colloch